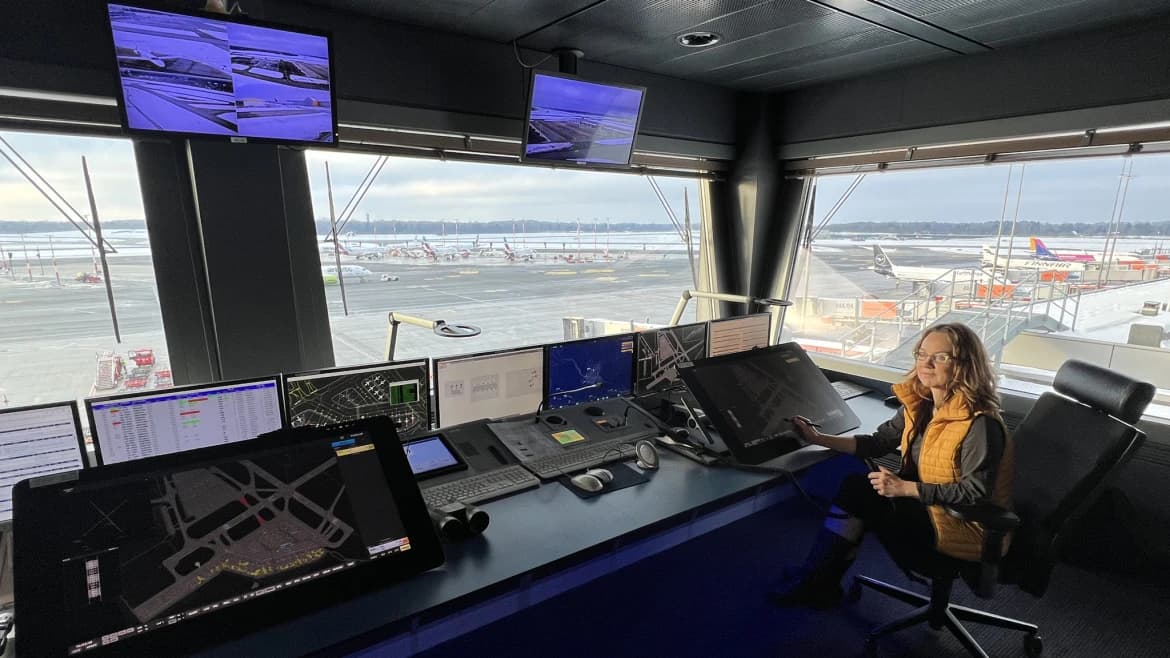
Flughäfen hinter den Kulissen: Die Vorfeldlotsin
Natalie Lüth sagt Crews, wo sie ihr Flugzeug parken dürfen und wie sie zügig wieder die Startbahn erreichen. Vom Aussichtsrestaurant im Obergeschoss des Hamburger Flughafens, wo Reisende und Besucher:innen sich am Büffet bedienen, sind es nur ein paar spezialgesicherte Türen in eines der Herzstücke des Flughafenbetriebs. Die Vorfeldkontrolle bietet die beste Aussicht auf das Flughafengelände, ähnlich einer Schiffskommandobrücke, mit Scheibenwischern für klare Sicht bei schlechtem Wetter. Hier arbeitet seit 30 Jahren Natalie Lüth. Die 54-jährige Hamburgerin wollte nach ihrer Ausbildung zur Fluglotsin in ihrer Heimatstadt bleiben und nicht nach Frankfurt ziehen. „Bei der Deutschen Flugsicherung (DFS) hätte ich wegziehen müssen, deshalb habe ich meinen Arbeitgeber gewechselt und 1994 beim Hamburger Flughafen als Vorfeldlotsin angefangen,“ erzählt sie. Ihr Arbeitsfeld ist die Apron Control, der flughafeneigene Kontrollturm, der den Verkehr auf dem Vorfeld überwacht und den Flugzeugen Rollwege und Parkpositionen zuweist. Gerade zu Spitzenzeiten kann es dort eng werden. Effiziente Abläufe sind Voraussetzung, um die Infrastruktur des Flughafens optimal zu nutzen. Früher rollten die Flugzeuge einfach im Uhrzeigersinn Eine eigene Vorfeldkontrolle gibt es am Flughafen Hamburg erst seit 1992. „Vorher gab es keine Fluggastbrücken, und die Flugzeuge rollten eigenständig je nach genutzter Start- und Landebahn im Uhrzeigersinn oder entgegen dem Uhrzeigersinn,“ sagt Lüth. “Vorher wurden die Abstellplätze der ankommenden Flugzeuge ausschließlich von der Verkehrszentrale geplant. Die Airlines wussten, dass wenn sie etwa auf Bahn 33 starten, sie dann im Uhrzeigersinn rollen. Es gab hier eine Art Insel, auf der die Flugzeuge geparkt haben.“ Bald aber wuchs der Flugverkehr so stark, dass mehr Parkpositionen gebraucht wurden, heute sind es am Flughafen Hamburg knapp 50 Stellplätze für Verkehrsflugzeuge und weitere für kleine Maschinen. Es wurde eine Instanz nötig, die das Zu- und Abrollen überwacht und koordiniert. Natalie Lüth war vor 30 Jahren die erste weibliche Vorfeldlotsin. „Als einzige Frau war das nicht immer angenehm, da einige Kollegen Vorurteile hatten. Aber die Zeiten haben sich geändert. Heute habe ich 21 Kolleg:innen, davon sind zehn Frauen.“ Vorfeldkontrolle ist Teamwork Und hier ist Teamwork gefragt. „Bei größerem Aufkommen wie an Wochentagen und zu Ferienbeginn sollten je Schicht vier Positionen besetzt sein“, so Lüth. „Zwei Vorfeldlotsen sind für eine sichere, geordnete und zügige Bewegungslenkung auf dem Vorfeld zuständig und dafür, dass die gelandeten Flugzeuge sicher zu ihrer Parkposition kommen und die abfliegenden gut zu ihrem Rollhalt an der Startbahn.“ Zwei Assistenzlotsen arbeiten dabei den beiden Vorfeldlotsen zu, die mit dem Funk beschäftigt sind. Die Assistent:innen nehmen alle von außen kommenden Informationen auf und geben sie an die neben ihnen sitzenden Vorfeldlotsen weiter. In den Funkpausen informieren sie sie über wichtige Ereignisse und nehmen auch Informationen von ihnen zur Weiterverarbeitung entgegen. Das hat Natalie Lüth in ihrer eben beendeten Schicht erlebt. „Wir hatten gerade einen medizinischen Notfall an Bord eines gelandeten Flugzeugs. Das bekam ich über Funk vom DFS-Fluglotsen im Tower mitgeteilt. Das gebe ich dann an den Assistenzlotsen neben mir weiter, der die Flughafenfeuerwehr, den Follow Me-Fahrer und die Bodenverkehrsdienste informiert. Die müssen alle Bescheid wissen.“ Die Vorfeldkontrolle erteilt die Rollerlaubnis zum Gate Vorfeldlotsen wie Natalie Lüth arbeiten in enger Abstimmung mit ihren Kolleg:innen von der DFS oben auf dem Tower, von dort werden die Flugzeuge durch die Luft und auf den Bahnen und Rollwegen bis kurz vor die Einfahrt aufs Vorfeld geleitet. „Am Übergang vom Pisten- zum Vorfeldbereich werden die Flugzeuge vom Tower zu mir auf die Vorfeldfrequenz geschickt. Die Pilot:innen müssen auch anhalten, ehe sie in meinen Zuständigkeitsbereich einrollen“, erklärt Lüth. „Sie müssen mich über Funk rufen und dann weise ich ihnen den Rollweg zur Parkposition zu. Ich kann dafür auch mit den DFS-Kolleg:innen auf dem Tower sprechen, damit sie mir das Flugzeug vielleicht auf einem anderen Rollweg zuführen, um den Rollvorgang so effizient wie möglich zu machen.“ Es kommt dabei nicht nur darauf an, mit der gerade gegebenen Situation umzugehen, sondern auch vorauszudenken. „Wenn wir uns nicht schon vorher Gedanken über die beste Verkehrslenkung am Boden machen würden, würden wir die Flugzeuge nicht so schnell zur Piste bekommen. Da könnten sonst andere Maschinen im Weg stehen oder ein Schlepperfahrer, der gerade ein Flugzeug bewegen will, das Rollen behindern“, weiß die erfahrene Vorfeldlotsin. Die Kopf- und Handarbeit kann keine Software ersetzen Trotz aller heute üblicher Computerhilfe gibt es für diese Bodenkoordination bisher keine Software. „Das ist unsere menschliche Koordinierungsleistung, vieles erkenne ich schon durch meinen Blick von oben und kann absehen und einplanen, was als Nächstes geschieht. Das könnte keine Software“, sagt Lüth. „Es gibt schon Programme, die für einen etwas effizienteren Ablauf sorgen, aber für die Verkehrsführung sind letztlich wir zuständig. Unsere Tätigkeit ist Kopf- und Handarbeit.“ Weil sich regelmäßig verschiedene Situationen, die auf unterschiedlichen Ebenen gelöst werden müssen, gleichzeitig zusammenballen, ist der Job in der Vorfeldkontrolle ein durchaus stressiger Beruf. „Genau dieser Stress macht mir ja Spaß“, sagt Natalie Lüth, und das schon seit drei Jahrzehnten. „Mich reizt, dass ich manchmal meinen Konzentrationsmodus auf Turbo stellen muss. Das ist eine Herausforderung, meiner Arbeit gewachsen zu sein, und so lange ich das kann, habe ich auch Freude an meinem Job.“ Auf den untenstehenden Link klicken, um den ganzen Artikel zu lesen.